DE HARRY KAO, YOMURA TECHNOLOGIES INC.
Decoração em molde (IMD/IML), também conhecida como moldagem por inserção de filme, sendo esta última uma melhor descrição para peças não decorativas. Este processo é por vezes chamado de In-Mold Label, é um processo semelhante utilizado principalmente para decorar recipientes, chávenas e vários recipientes. A técnica é o processo de decoração de uma peça moldada por injeção com um filme decorado durante o processo de injeção. O rótulo passa a ser parte integrante do produto final, criando um item totalmente decorado na superfície visual ou parcialmente como um rótulo num recipiente. Neste processo, uma etiqueta pré-impressa ou filme decorado é inserido no molde de injeção de plástico aberto e mantido no lugar mecanicamente, eletrostaticamente, por gravidade ou a vácuo. Quando o molde é fechado, a resina plástica é novamente injetada no filme, encapsulando-o permanentemente na peça acabada. Antes do aparecimento do IMD, existiam duas opções básicas para a decoração de peças moldadas, a serigrafia e a colagem de etiquetas na peça. Ambas as técnicas não conseguem igualar a flexibilidade e a durabilidade do IMD. A técnica permite designs mais imaginativos que não só melhoram a decoração, como também proporcionam funcionalidade. A técnica adapta-se facilmente a superfícies inteligentes, teclas táteis, produtos resistentes à água, circuitos eletrónicos e até componentes óticos que podem ser integrados de forma económica. A maioria de todos os filmes são impressos em segunda superfície, a impressão na superfície primária é menos durável. A impressão da segunda superfície pode ser de uma só cor muito simples até padrões de múltiplas passagens muito complexos que simulam superfícies de mármore e incluem filtros óticos funcionais. A impressão da segunda superfície contribui muito para a durabilidade do produto e é um fator importante na seleção do IMD. A peça pode ser passiva ou ativa, com traços e superfícies eletroluminescentes incluídas no filme, a frente morta, os filers, a sobremoldagem e a galvanoplastia seletiva são também opções de design.
O processo IMD tem essencialmente 3 etapas: 1. Impressão, 2. Formação, 3 injecção inversa. A etiqueta no molde normalmente salta o passo 2, uma vez que a etiqueta é plana e pressionada contra o molde.
Impressão - A serigrafia é o método mais comum para impressão de filmes, digital e offset, são menos comuns A impressão digital UV está a ganhar terreno rapidamente e cumprirá a longa promessa de poder ter um gráfico diferente em cada moldado parte sem qualquer aumento significativo do custo. A impressão foi muito além dos simples gráficos impressos em tela que imitam os designs de etiquetas existentes; são agora comummente produzidos padrões complexos que proporcionam uma representação bastante boa da fibra de carbono e das superfícies de mármore. Com a nova geração de tintas condutoras, a capacidade de imprimir componentes eletrónicos em 3D, um processo altamente desejado, mas muito dispendioso de utilizar, tornar-se-á agora comum.
Tintas - O processo IMD requer tintas especiais, as que não são especialmente formuladas irão rachar e amarelecer quando processadas. Devem ser flexíveis e resistentes à lavagem quando esticados. A impressão não é uniforme em todo o filme, sendo frequentemente necessário imprimir múltiplas camadas em zonas de grande estiramento e onde a resina colide com o filme ao sair da porta. A última camada a ser impressa é o revestimento anti-lavagem, dependendo da localização da porta e da pressão de injeção, podem ser necessárias várias camadas do anti-lavagem para evitar que a tinta seja removida da superfície do filme. Novos desenvolvimentos na tecnologia de tintas condutoras permitir-lhes-ão suportar os rigores do processamento no molde e ainda manter as suas propriedades dielétricas. Os painéis tácteis tornaram-se o método preferido de introdução de dados num dispositivo e o nível de integração aumentará com a melhoria na impressão de filmes IMD. Existem mais dois passos necessários após a impressão dos gráficos; A camada final a imprimir é um promotor de adesão, a resina injetada na maioria dos casos não formará naturalmente uma ligação ao filme impresso. A ligação é extremamente importante, uma vez que a delaminação é possível ao longo de um período de tempo se o filme for exposto a ciclos térmicos ou a contacto. Os adesivos utilizados para esta aplicação são ativados termicamente e requerem energia térmica suficiente para que o adesivo atinja a temperatura de transição vítrea. É necessária alguma experimentação com uma peça e com a ligação adesiva para garantir que a ligação é satisfatória. A temperatura do molde, o tempo de permanência e a temperatura do material de injeção desempenham um papel crítico para garantir que é feita uma ligação satisfatória.
Filmes - Existem diversas opções de filmes, dependendo da aplicação específica para a qual o produto está a ser concebido.
PA (poliamida) Estes filmes possuem uma excelente resistência química, elevada transparência, boa durabilidade mecânica e elevada temperatura de deflexão térmica. São adequados para utilização com ABS, PC/ABS, PC e materiais de substrato semelhantes.
O filme de PC (policarbonato) possui muito boas propriedades ópticas, pode ser facilmente termoformado, tem uma elevada resistência ao impacto e uma boa resistência ao calor. O policarbonato é amorfo e tem uma baixa resistência química.
ABS (Acrilonitrilo butadieno estireno) Estes filmes têm uma resistência ao impacto muito boa e são naturalmente translúcidos, oferecem uma boa relação custo-benefício, assim como o PC têm uma baixa resistência química.
PP ( Polipropileno) Apresentam uma ótima relação custo-benefício e uma excelente resistência química. São utilizados com mais frequência na rotulagem IML de recipientes.
PMMA (polimetilmetacrilato) Apresenta uma excelente resistência ao risco superior ao PA e ao PC quando não revestido. É altamente transparente e adequado para aplicações ópticas quando comparado com o PC e PA o nível de desempenho mecânico é menor.
PET (Poliéster) Possui uma excelente estabilidade térmica, boas propriedades mecânicas, elevada resistência, boa estabilidade dimensional e clareza óptica. Estes filmes são os mais utilizados em produtos de grande consumo.
Tratamentos de superfície em filmes como revestimento duro, antirreflexo, antiembaciamento, acabamento acetinado e mate estão disponíveis nos fornecedores. Deve-se ter o cuidado de evitar arestas vivas ao projetar uma peça que irá utilizar película com revestimento rígido. O revestimento duro tende a fissurar quando formado em torno de um raio pequeno;
Termoformação - O filme impresso é então formado normalmente para o processo IMD por formação térmica por pressão. Uma folha impressa é aquecida e depois forçada para dentro de um molde fêmea, evacuando o ar do mesmo. O material assume então a forma do molde, permitindo a formação de maiores detalhes na peça do que a tradicional moldagem a vácuo. O processo de conformação provoca um estiramento no material que pode resultar em gráficos deformados ou mal posicionados. Para compreender a quantidade de estiramento que o filme está a sofrer, é processada uma etiqueta impressa com um padrão de grelha. As variações no padrão de grelha após o processamento podem ser facilmente observadas. Isto permite ao designer gráfico ajustar o gráfico que pode ser afetado pelo alongamento. A profundidade de estiramento é limitada pela configuração da peça e, aparentemente, pela capacidade de processamento do moldador, com um bom processador, são possíveis profundidades de estiramento de 25 mm. As tintas são também um fator na quantidade de deformação que pode ser tolerada no processo de conformação térmica. As tintas UV modernas são muito mais resistentes ao estiramento criado pelo processo de formação e estarão sujeitas a alterações na densidade da cor se forem ultrapassadas as suas limitações.
Cortar – A peça conformada necessita de ser recortada, isto é feito antes da inserção no molde ou após a fase de injeção. O corte não pode ser feito com precisão com uma matriz de aço; deve ser criada uma ferramenta de placa correspondente de alta qualidade para cortar o filme com precisão. Para produção de grande volume, o filme pode ser alimentado na estação de formação térmica em forma de rolo e pós-cortado. Em algumas aplicações, o formato formado pode ser obtido por um processo de conformação a frio, da mesma forma que se produz uma peça metálica estampada e estirada. Todo o processo de impressão do papel, estampagem, injeção e recorte é totalmente automatizado. O processo IMD está a tornar-se mais automatizado com a impressão em lote, o corte automático e a retroinjeção a serem realizados pela robótica. O processo deve ocorrer sempre em salas limpas, sujidade no filme ou no molde pode causar perda significativa de rendimento.
Operações secundárias.
As operações pós-processamento, como a sobremoldagem, a galvanização seletiva e a impressão, são facilmente realizadas. Abaixo estão as Figuras 1,2 e 3. Aqui está uma breve descrição do processo que atinge os resultados mostrados
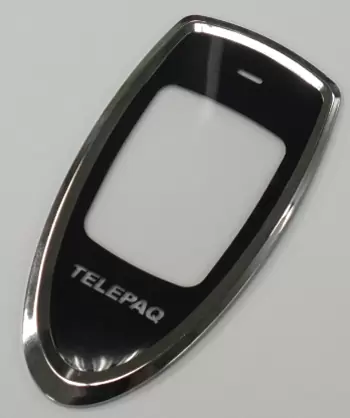
Fig 1 é uma moldura para um telefone de mão. À primeira vista parece ser uma peça relativamente simples de fabricar. O primeiro processo é a Etiqueta IMD contendo a janela e o fundo preto, o material selecionado para a peça é o Policarbonato. A etiqueta é então inserida no molde e moldada com ABS prateado, esta é a borda brilhante da imagem. O processo de revestimento do ABS é bem conhecido. Para chapear o ABS a sua superfície deve ser modificada com uma solução de ataque químico. A solução de ataque é baseada em ácido crómico e não ataca o policarbonato. Após o ataque, a superfície é ativada ou preparada com uma solução contendo sais de estanho e paládio. A superfície do ABS é então revestida com níquel ou cobre. A etapa final é a galvanoplastia com tecnologia convencional. Como o PC não foi gravado, não pode ser revestido, resumindo, este é o processo de revestimento seletivo.
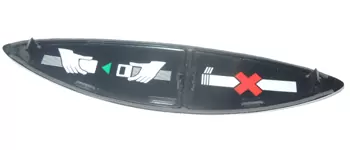
Fig 2 A imagem abaixo é um sinal familiar para quem já viajou de avião. Esta é a vista traseira, a parte frontal não é mostrada, é um painel frontal morto, os gráficos não podem ser vistos até que o sinal seja iluminado. A superfície frontal é impressa em tela numa cor que combina com a estrutura circundante e é translúcida. O verso é uma tela impressa com gráficos translúcidos. O fundo preto é impresso para evitar a transmissão de luz. A etiqueta é então injetada novamente com policarbonato transparente para formar a peça acabada.
O IMD, que antes era uma opção cara para os designers de produtos, tornou-se uma opção muito eficaz e com preços razoáveis. A qualidade é muito superior à de uma peça moldada decorada por serigrafia ou tampografia e/ou com uma etiqueta autocolante fixada numa superfície plana. O processo pode agora fornecer opções complexas a serem consideradas pelo designer. Podem adicionar um elevado nível de funcionalidade, gráficos complexos, funções óticas, mecânicas e elétricas numa montagem independente. Melhorias em filmes, tintas, adesivos e eletrónica continuam a ser feitas. O futuro do processo IMD é risonho com a introdução da tecnologia de superfícies inteligentes.