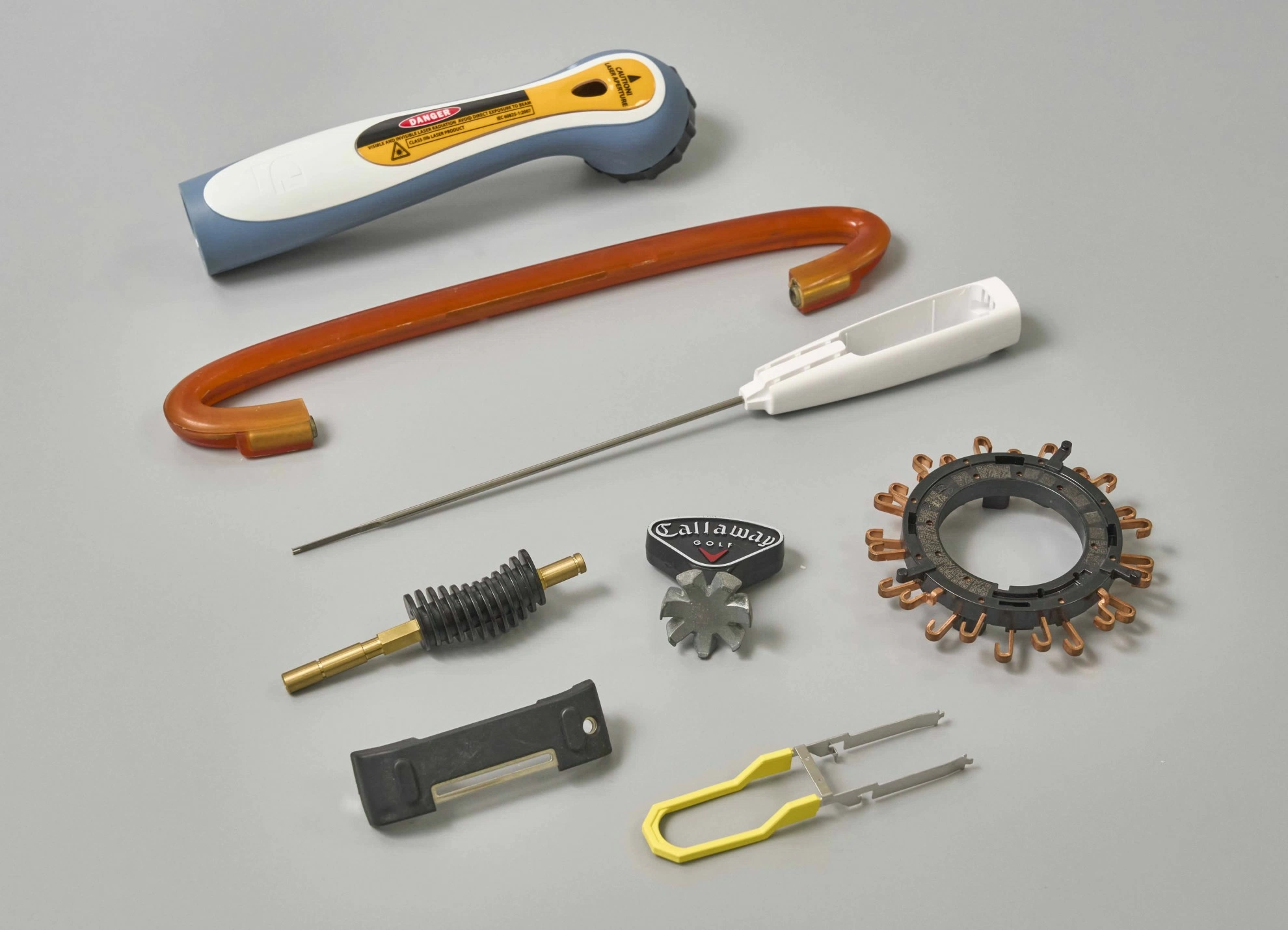
Insert-Molding: Integrating
Materials for Enhanced Performance
Explore the possibilities with Yomura's Insert Injection Molding technology - seamlessly integrating metal, plastic, or ceramic inserts into plastic components for improved structural integrity and enhanced functionality. Contact us today to unlock new possibilities for your products.
CONTACT USThe Insert Molding Process
Insert Placement
The process begins by placing the desired insert, such as metal, plastic, or ceramic, into the mold cavity.
Plastic Injection
A carefully selected plastic material is injected directly over the insert, encapsulating it within the molded component.
Unified Integration
The result is a single, unified part with the insert securely embedded within the plastic matrix, creating a seamless integration.
A Wide Range of Materials
Engineering Plastics
Offering improved wear resistance, tensile strength, and weight reduction.
more...
- TPR + Metal Frame(3C Mechanical Parts)
- ABS + Al. Die Cast (Sports/ Medical) Eng.
- Plastic + Patting Pin/Eng. Plastic + Wireframe (Connector)
- Eng. Plastic + Copper Pin/Contact (Precision Electronic Component)
Thermoplastic Rubbers (TPRs)
Provide enhanced flexibility and durability, ideal for specific applications.
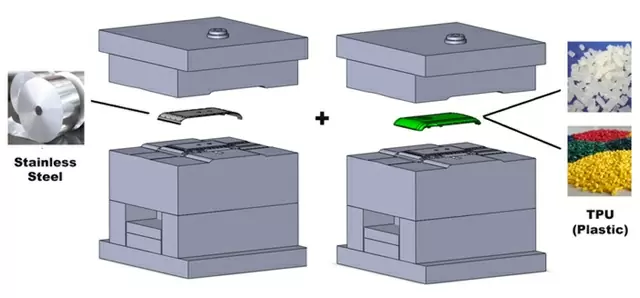
Applications of Insert Molding
Consumer Electronics
Integrating metal frames, plated copper pins, and sockets for enhanced durability and improved electrical connectivity.
Automotive
Combining metal die-cast inserts with plastics for lightweight, high-strength structural components.
Sports and Medical
Embedding metal or ceramic inserts into plastic components for enhanced performance and durability.
Electrical and Electronics
Encapsulating wire frames, copper pins, and contacts into plastic components for precise electrical connections and insulation.
Benefits of Insert Molding
Reduced Assembly and Labor Costs
Integration of multiple components minimizes the need for separate assembly processes, lowering costs and improving efficiency.
Increased Design Flexibility
Allows for virtually unlimited configurations, enabling complex geometries, intricate circuit paths, and innovative product designs.
Reduced Size and Weight
Elimination of fasteners and connectors, combined with the strategic use of lightweight materials, results in smaller and more compact designs.
Increased Reliability
Inserts securely encapsulated within the plastic matrix ensure improved resistance to shock, vibration, and environmental factors, ensuring long-lasting performance.
High-Quality Solutions
Precision
Exacting precision in every molded part, ensuring high-quality results.
Innovation
Continuous innovation in materials and processes to deliver cutting-edge solutions.
Efficiency
Streamlined processes for efficient production and cost-effective solutions.
Unlock New Possibilities
Enhanced Performance
Unlock new possibilities for your products with enhanced performance and durability.
Cost-Effective Solutions
Explore cost-effective solutions that meet the demanding requirements of diverse industries.
Innovative Designs
Realize innovative product designs, intricate circuit paths, and complex geometries with insert molding technology.